As it is difficult to estimate the size of a company and its production for more than 5 years in advance, capacity problems often arise after years of operation. Expansion options are limited for most companies and the only option available is to operate within their capabilities. One way to find out your reserves is to perform a capacity audit and a logistics audit. These audits point to the potential for increasing production capacity while reducing production and storage facilities.
Logistics audit
- Collection of quantitative and qualitative data from key stakeholders (transport, warehouse, purchasing, manufacturing, sales, customer and IT departments, or specific company departments) - analysis of the current situation.
- Analysing and creating individual maps of processes, documents and physical flows - creating a clear process to identify shortcomings and possible risks in society.
- Creating specific measures and modifying current process maps. Assess the potential risks of proposals in order to eliminate incorrect implementation of changes.
- The information obtained and the measures created will be used to analyse logistics costs and potential savings arising from the implementation of the proposed measures.
Capacity audit
- Mapping of ongoing periods of activity - the result will be a shortening of production cycles.
- Tracking of duplicate and inefficient activities - the result will be workflow optimization.
- Revealing bottlenecks in production processes - the result will be an optimization proposal.
- Analysis of capacity options of machines and production lines - the result will be more efficient capacity of equipment.
- Quantitative, time and service analysis of consumption - the result will be a proposal for consumption standards.
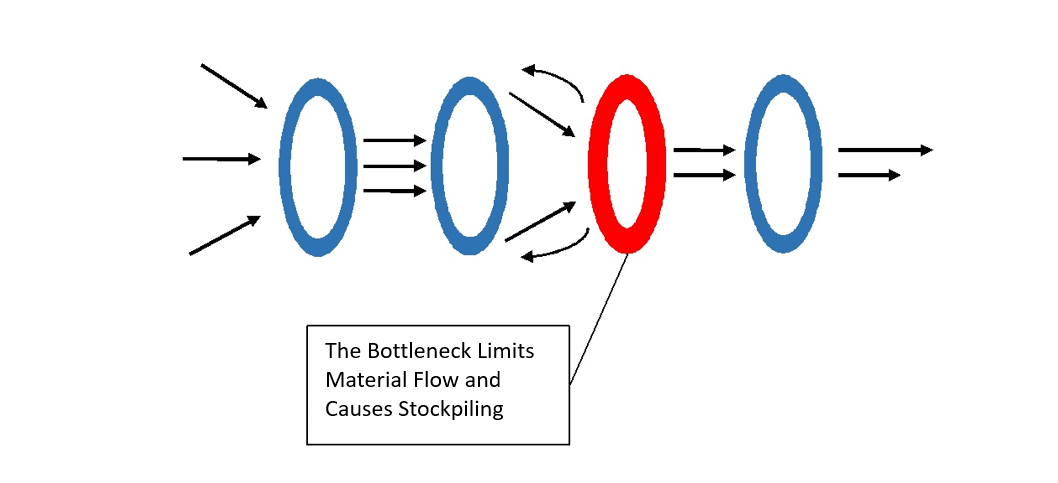
Picture: Show bottlenecks in your organization
Possibilities of using capacity audit and logistics audit in:
- Expansion of production and production capacity.
- Optimal placement of new machines and equipment.
- Reducing the size of storage space and excessive handling.
- Verification of capacity options of suppliers.
- Optimization of material flows in production.